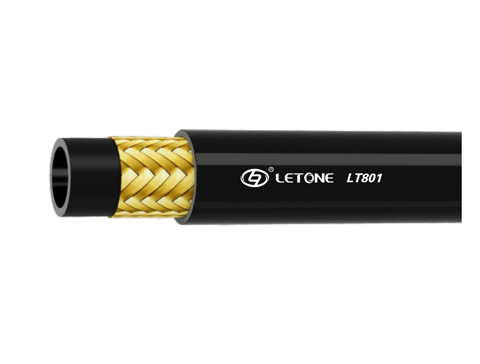
High Pressure Resistant Material Hose
In industrial production and engineering applications, the demand for fluid transmission in high-pressure environments is increasing day by day. As a key connecting component, high-pressure resistant hoses have become an indispensable part of the petrochemical, mechanical manufacturing, aerospace and other fields due to their unique flexibility and reliability. This article will analyze the technical connotation and industrial value of high-pressure hose from three aspects: material and structure, core functions, and practical application scenarios.
1、 Design and Material Innovation of High Pressure Resistant Hose
High pressure resistant hose is not a simple upgraded version of ordinary rubber hose, but an engineering material product that achieves performance breakthroughs through multi-layer composite structure. Its typical structure includes three parts: inner adhesive layer, reinforcement layer, and outer adhesive layer:
The inner rubber layer is usually made of corrosion-resistant synthetic rubber (such as nitrile rubber, fluororubber) or polyurethane material, which directly contacts the transmission medium to ensure chemical stability;
The reinforcement layer is the core source of pressure bearing capacity, which adopts high-density steel wire weaving or winding structure, and forms a mechanical support network through 45 ° cross arrangement. Some high-end products also add aramid fibers to enhance tensile resistance;
The outer rubber layer is made of wear-resistant and anti-aging rubber or thermoplastic elastomer, and the surface is often designed with anti-static texture or flame retardant coating to cope with complex working conditions.
2、 Functional features: Breaking through the limitations of traditional pipelines
The core value of high-pressure hoses lies in their ability to overcome the rigidity and installation limitations of traditional metal pipelines, while maintaining safety and stability in high-pressure environments
Dynamic pressure bearing capacity: The hose certified by ISO 18752 standard can operate continuously at a working pressure of 70MPa, with a burst pressure of more than 4 times the working pressure, meeting the pulse pressure impact requirements of hydraulic machinery;
Three dimensional flexibility: The bending radius can reach 5-8 times the diameter of the pipe, supporting flexible pipe layout in complex spaces, such as the three-dimensional pipeline system of deep-sea oil platforms;
Environmental adaptability: It can maintain elasticity within the temperature range of -50 ℃ to 150 ℃, and special models can even withstand instantaneous high temperatures of 300 ℃ (such as fire hoses);
Media compatibility: special formulations were developed for different transmission media (acid, oil, liquefied gas). A chemical enterprise customized PTFE lined hose successfully solved the problem of long-distance transportation of 98% concentrated sulfuric acid.
3、 Cross industry application scenarios and technology extensions
The application of high-pressure hoses has already broken through the traditional industrial field and extended to more high-precision and cutting-edge scenarios:
In the field of energy extraction, the fracturing hose used in shale gas extraction needs to transport sand containing fracturing fluid at a pressure of 70MPa. It adopts a structure of double-layer steel wire winding and lining with polyetheretherketone, and its service life is three times longer than conventional products;
Intelligent manufacturing industry: The pulse resistant hose mounted on the hydraulic arm of industrial robots is reinforced with a composite structure of spiral steel strip and aramid fiber, which can withstand 200 pressure fluctuations per minute