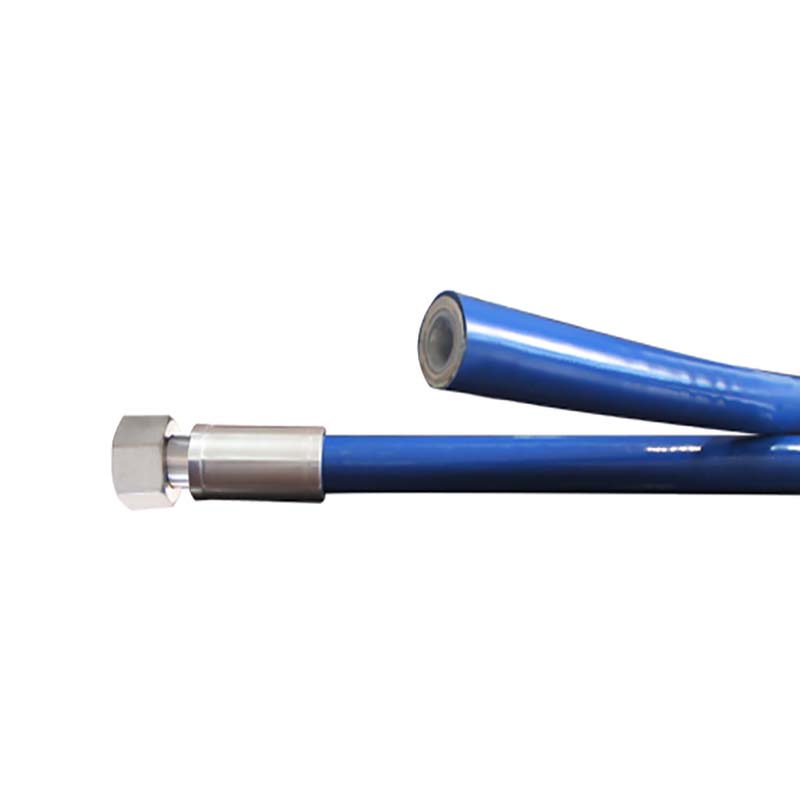
Analysis of the structural characteristics, functional advantages, and application scenarios of high
As a key component for transmitting power in industrial equipment, the selection of hydraulic hoses directly affects the safety and efficiency of the system. With the continuous development of industrial technology, the application fields of hydraulic hoses are becoming increasingly widespread, covering almost all occasions that require hydraulic transmission, from engineering machinery to aerospace, from metallurgical equipment to petrochemicals. Therefore, it is particularly important to have a correct understanding and selection of hydraulic hose models.
The hydraulic hose model is usually composed of a series of letters and numbers, which represent key parameters such as the structure, material, pressure rating, and size of the hose. Taking the common "1SN-16-20" model as an example, "1SN" indicates that the type of hose is a single-layer steel wire braided hydraulic hose, "16" represents that the inner diameter of the hose is 16 millimeters, and "20" represents that the working pressure is 20 MPa. Different manufacturers may have different naming conventions, but they generally include these core information.
Structurally, hydraulic hoses are mainly divided into two categories: braided and wound. Braided hydraulic hoses are usually composed of an inner rubber layer, a reinforcement layer, and an outer rubber layer. The reinforcement layer is woven from steel wire or fiber and has good flexibility and bending resistance. The reinforcement layer of the winding hydraulic hose adopts steel wire spiral winding, which has higher pressure bearing capacity, but the bending performance is relatively poor. In practical applications, it is necessary to select the appropriate structural type based on parameters such as working pressure, pulse frequency, and bending radius.
Material selection is an important consideration factor in determining the type of hydraulic hose. The inner rubber layer material needs to be compatible with the conveying medium, and common materials include NBR (nitrile rubber), EPDM (ethylene propylene diene monomer rubber), etc. NBR is suitable for mineral oil-based hydraulic oil, FKM has better high temperature resistance and chemical corrosion resistance, and EPDM is suitable for special media such as water ethylene glycol. The outer rubber layer needs to have the characteristics of wear resistance, weather resistance, aging resistance, etc., and is usually made of CR (neoprene) materials.
Pressure rating is a key parameter in hydraulic hose models, typically expressed in MPa or psi. When choosing a pressure level, not only should the working pressure of the system be considered, but also factors such as pulse pressure and peak pressure should be taken into account. Generally speaking, the working pressure should not exceed 75% of the rated working pressure of the hose to ensure safety margin. For high-pressure applications, such as hydraulic systems in construction machinery, it is usually necessary to choose high-pressure hoses with 4 or 6 layers of steel wire winding.
The size parameters include inner diameter, outer diameter, and length. The selection of inner diameter needs to consider flow requirements, as a too small inner diameter can lead to high flow velocity and increase pressure loss; An excessively large inner diameter will increase the system volume and cost. The outer diameter is related to the pressure bearing capacity of the hose, and usually the higher the pressure rating, the larger the outer diameter. The length selection should consider the installation space and the minimum bending radius of the hose to avoid early failure caused by excessive bending.
The temperature range is also a factor to consider when choosing a hydraulic hose model. Different materials of hoses have different temperature resistance properties. NBR materials are usually used in the range of -40 ℃ to+100 ℃, while PTFE materials can withstand higher temperatures. Hydraulic systems operating in extreme temperature environments require special attention to the temperature adaptability of hoses.
In addition to these basic parameters, hydraulic hose models may also include other special performance indicators, such as anti-static performance, flame retardant performance, food grade certification, etc. For example, hydraulic hoses used in flammable and explosive environments such as coal mines need to have anti-static and flame-retardant properties; The hoses used in food processing equipment need to comply with food grade certification standards such as FDA.
In practical applications, the selection of hydraulic hoses also needs to consider factors such as pulse life, bending radius, and joint type. Pulse life refers to the service life of a hose under alternating pressure, which is closely related to the structure and material of the reinforcement layer. A bending radius that is too small can accelerate the fatigue damage of the hose, so it is important to ensure that it is not less than the minimum bending radius during installation. The type of joint needs to match the system interface, commonly including 24 ° cone seal, flange connection, and sleeve type connection.
With the development of technology, new types of hydraulic hoses continue to emerge. If the working pressure of ultra-high pressure hydraulic hoses can reach over 100MPa, they are suitable for special engineering machinery; Lightweight hoses are made of new composite materials, which reduce weight while ensuring strength; The intelligent hose is equipped with built-in sensors that can monitor real-time parameters such as pressure and temperature. These innovative products provide more possibilities for the design and application of hydraulic systems.
Maintenance is also an important part of extending the service life of hydraulic hoses. Regularly inspect the surface of the hose for any abnormal phenomena such as cracks, bulges, leaks, etc; Avoid contact between hoses and sharp objects; Keep the hose clean to prevent oil contamination and corrosion; Pay attention to anti freezing measures when using in cold environments. Proper maintenance can significantly improve the service life and system reliability of hoses.
In short, the selection of hydraulic hose models is a systematic engineering process that requires comprehensive consideration of various factors such as working medium, pressure, temperature, and environment. Only by fully understanding the meanings of various model parameters can the most suitable hydraulic hose be selected for specific application scenarios, ensuring the safe, efficient, and reliable operation of the hydraulic system. With the advancement of industrial technology, the technical standards for hydraulic hoses are constantly being updated. Engineering and technical personnel need to continuously pay attention to industry trends and master the latest product information and technical specifications.