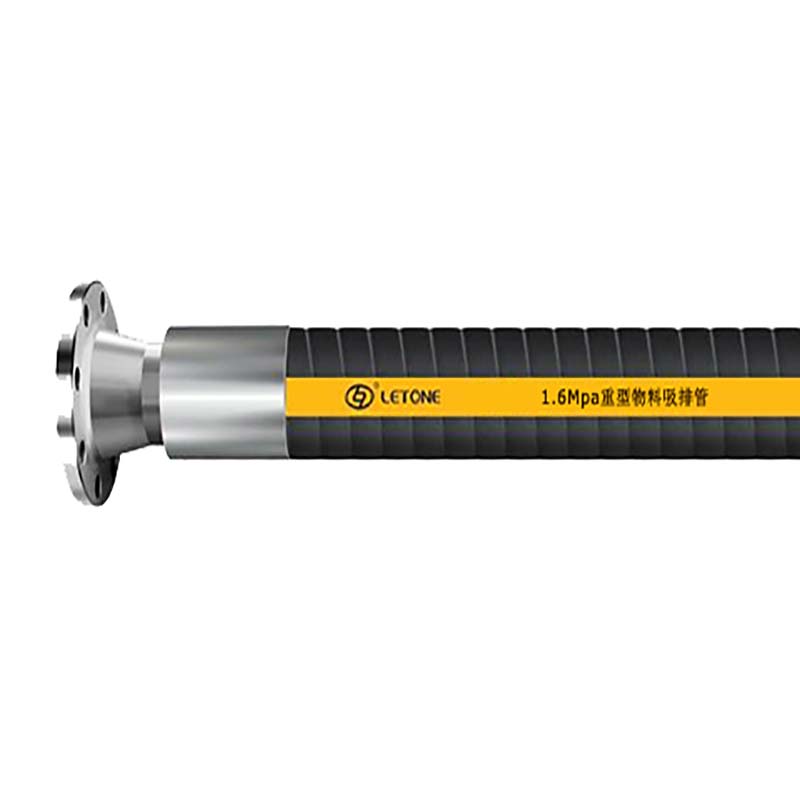
Application scenarios of compression type assembly
As a key hydraulic connecting component widely used in engineering machinery, mining equipment, petrochemicals and other fields, the performance of the buckle type rubber hose assembly directly affects the safety and reliability of the entire hydraulic system. This article will systematically analyze this professional field from the aspects of technical principles, production processes, market status, and future development trends.
1、 Technical Principles and Structural Design
The buckle type rubber hose assembly consists of an inner rubber layer, a reinforcement layer, an outer rubber layer, and a metal joint. Its core technology lies in achieving a leak free connection between the rubber hose and the joint through precision buckle technology. According to product information from Baidu Aiqicha, modern compression type assemblies use multi-layer steel wire weaving or winding structures, with a working pressure of over 35MPa and a burst pressure of four times the working pressure. Among them, the inner rubber layer is usually made of oil resistant synthetic rubber, such as NBR or HNBR materials; The reinforcement layer is woven with high carbon steel wire at a specific angle to form a pressure bearing skeleton; The outer rubber layer shall be wear-resistant and anti-aging.
In terms of joint design, patent document (CN06120113569183) reveals an innovative 24 ° conical sealing structure, which forms a triple sealing barrier during the crimping process through the cooperation of the conical surface and O-ring: firstly, the mechanical interlocking between the metal joint and the rubber hose, secondly, the self sealing effect generated by the compression of the inner rubber layer, and finally, the interference fit between the conical surface and the matching parts. Compared to traditional planar seals, this structure has improved pressure resistance by about 30%.
2、 Production process and quality control
The data shows that the production of high-quality buckle pressure rubber hose assemblies requires 12 key processes:
1. Pre treatment of rubber hoses: Laser caliper is used to control the cutting accuracy of rubber hoses, with a tolerance controlled within ± 0.3mm
2. Joint assembly: Use liquid nitrogen cold shrinkage process to achieve interference fit and avoid damage to the inner wall of the hose
3. Compression molding: The six petal mold radial compression technology ensures 360 ° uniform force, and the compression rate is strictly controlled within the range of 15% -18%
4. Stress test: Conduct a 100% pressure holding test at 1.5 times the working pressure, with a duration of no less than 3 minutes
3、 Analysis of Industry Application Status
According to the engineering case, the buckle type rubber hose assembly presents differentiated demand characteristics in the following areas:
-Construction machinery field: accounting for 42%, requiring the assembly to have anti pulse performance (≥ 1 million pulse tests)
-Coal mine hydraulic support: requires MA certification, flame retardant performance requirement oxygen index ≥ 28%
-Ocean platform: Special polytetrafluoroethylene rubber material can withstand extreme environments of -40 ℃~150 ℃
5、 Key points of use and maintenance
Based on industry practice, provide the following professional advice:
1. Installation specifications: The bending radius should not be less than 7 times the outer diameter of the hose, and the twisting angle should be controlled within 5 °
2. Failure warning: When the outer adhesive layer cracks (crack depth>1mm) or the joint displacement exceeds 10% of the original position, it must be replaced immediately
3. Storage conditions: The temperature should be maintained between -15 ℃ and 40 ℃, avoiding storage in the same warehouse as the ozone generator
It should be emphasized that assemblies with different pressure levels are strictly prohibited from being mixed and used. An accident analysis report indicates that approximately 37% of hydraulic system failures are caused by the misuse of low-pressure assemblies for high-pressure conditions. It is recommended to conduct a system stress test every 500 working hours and establish a complete lifecycle management file.