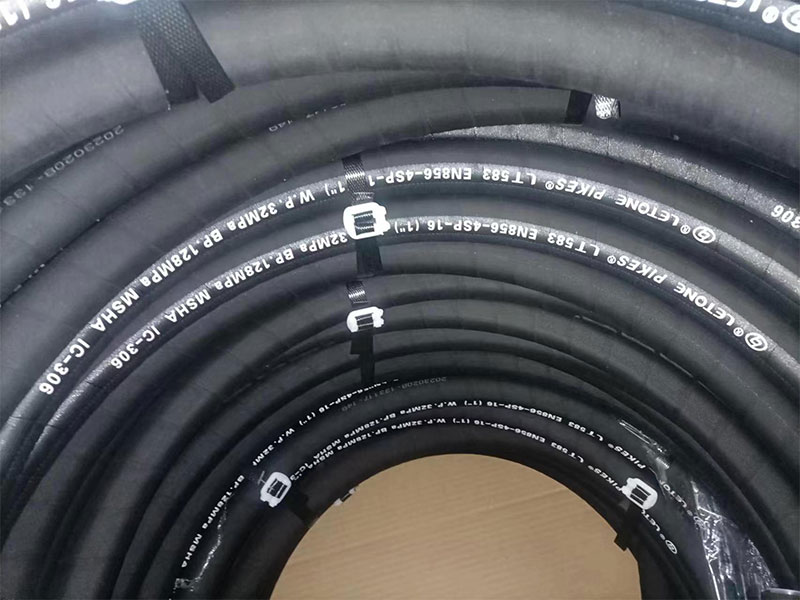
Performance comparison of high-pressure hoses
As a key component of oil and gas drilling, the production process of rotary drilling hoses must strictly follow industry standards (such as API 7K, ISO 6802), involving precision material selection, multi-layer composite structure forming, and strict quality control. The following is its detailed production process:
1. Raw material preparation and pretreatment
Rubber mixing:
Inner rubber layer: Made of nitrile rubber (NBR) or hydrogenated nitrile rubber (HNBR) with excellent oil resistance, added with additives such as carbon black and anti-aging agents, and mixed evenly through a mixer. The mixing temperature is controlled at 80-120 ℃ to ensure that the rubber material reaches a Mooney viscosity (ML (1+4) 125 ℃) of 50-70.
Outer rubber layer: UV resistant chloroprene rubber (CR) is selected, and anti ozone agents and wear-resistant fillers (such as silica) are added. After mixing, the rubber material needs to be left to stand for 24 hours to eliminate internal stress.
Enhanced material processing:
High strength steel wire (tensile strength ≥ 2500 MPa) is treated with phosphate coating to enhance its adhesion with rubber, and then twisted into steel wire bundles using a splicing machine, with a diameter accuracy controlled within ± 0.05mm.
2. Extrusion molding of inner rubber layer
Extrusion process:
The mixed rubber material is extruded into a tubular inner rubber layer through a cold feed extruder at 90-110 ℃.
Inner diameter accuracy control: Real time monitoring using a laser caliper, with a tolerance range of ± 0.5mm.
Inner rubber layer thickness: adjusted according to the hose specifications (such as 6 inches/8 inches), usually 3-5mm, to ensure wear resistance and impermeability.
3. Reinforcement layer wrapping/weaving
Wire winding:
Spiral winding machine: Pre treated steel wire bundles are spiral wound at an angle of ± 55 ° on the outer surface of the inner adhesive layer, with the number of layers determined according to the pressure level (e.g. 4 layers correspond to 35 MPa, 6 layers correspond to 52 MPa).
Tension control: The tension of each steel wire is maintained at 200-300N to ensure even winding without gaps.
Conductive layer integration: Copper wires (diameter 0.5-1mm, resistance ≤ 0.1 Ω/m) are embedded between the inner adhesive layer and the reinforcement layer to dissipate static electricity.
4. Coating and molding of outer adhesive layer
Secondary extrusion:
Wrap a chloroprene rubber outer layer on the outside of the reinforcement layer, with an extrusion temperature of 100-130 ℃ and a thickness of 2-4mm.
Surface treatment: The outer adhesive layer is pressed with diamond patterns or coated with wear-resistant tape (polyurethane material) to enhance its resistance to mechanical wear.
Identification printing: Mark the hose model, pressure rating, and production batch number through laser engraving or heat transfer printing.
5. Sulfurization process
Continuous vulcanization (CV):
The hose enters the vulcanization tank and is vulcanized for 20-30 minutes under high temperature and high pressure (150-160 ℃, steam pressure 1.5-2.0 MPa) to crosslink and solidify the rubber, and the layers are tightly bonded.
Sulfurization curve monitoring: Real time recording of temperature time curve to ensure that the vulcanization degree reaches 90% or above (determined by T90 index).
Segmented vulcanization: For ultra long hoses (such as single hoses over 30 meters), segmented vulcanization is used, and additional pressure is required in the overlapping area of the interface to ensure adhesive strength.
6. Flange joint assembly
Joint selection:
According to the API 7K standard, forged alloy steel flanges (such as AISI 4130) are selected, and the surface is galvanized or sprayed with epoxy resin for corrosion protection.
Thermal sulfurization mold:
Place the flange joint and hose end into the mold, inject uncured rubber material, and apply pressure vulcanization at 140 ℃ for 45 minutes to form a seamless connection.
Torque test: After assembly, the joint must pass a 40000 N · m torque test without looseness or leakage.
7. Finished product testing and quality control
Stress testing:
Static pressure test: Fill water and increase the pressure to 1.5 times the working pressure (such as testing a 52 MPa hose to 78 MPa), and hold the pressure for 3 minutes without any leakage.
Pulse test: Conduct 1 million pressure cycles (35 MPa → 0 MPa) according to ISO 6802 standard, with a frequency of 1 Hz and no cracks or bulges.
Conductivity testing: Measure the resistance between joints to ensure it is ≤ 1 Ω and meets explosion-proof requirements.
Appearance and dimensional inspection: Use an industrial endoscope to check the smoothness of the inner wall, and measure the thickness deviation of each layer with a caliper (within ± 0.3mm).
8. Packaging and Storage
Coiling and shaping: The hose is coiled on a steel drum with the minimum bending radius (1.5 times the pipe diameter) to avoid permanent deformation.
Protective packaging: Cover the end with a plastic sheath, wrap the outer layer with moisture-proof film, and put in a desiccant.
Storage conditions: Store in a cool and shaded warehouse (temperature -10~35 ℃, humidity ≤ 60%), away from ozone sources.