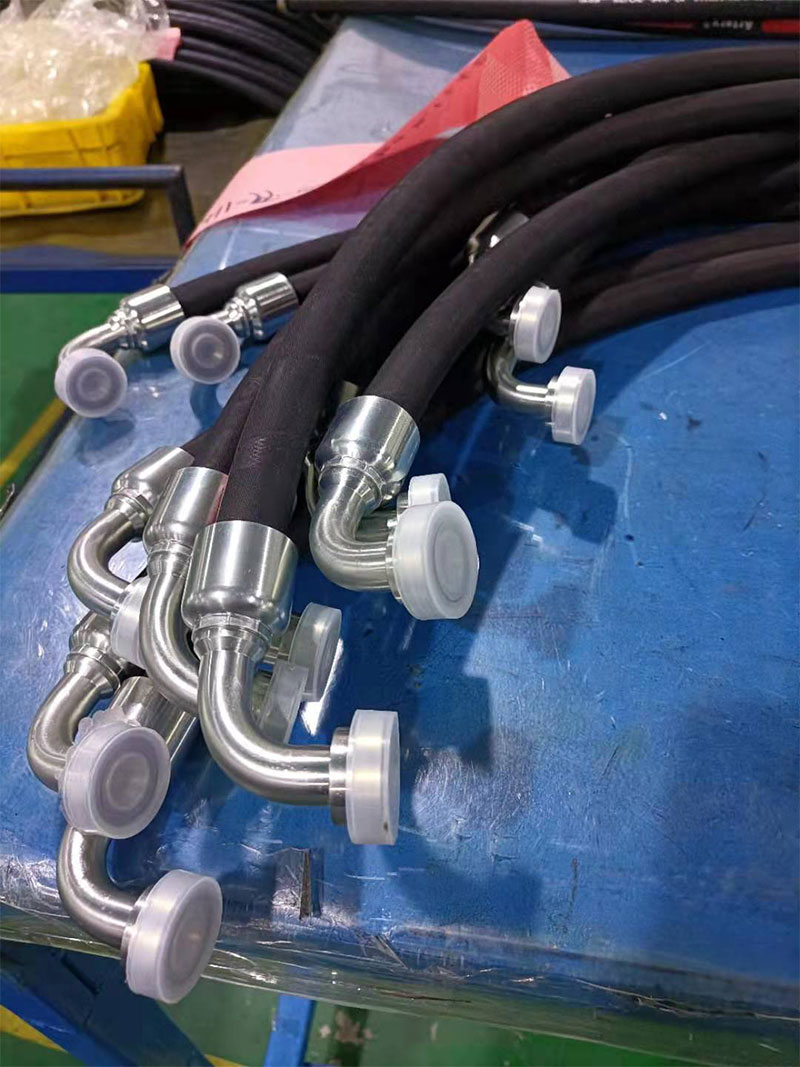
Structural analysis of mining rubber hose
In mining, transportation, and beneficiation processes, the Mining Large Diameter Hose Assembly is the core component that connects equipment and medium transportation. This type of rubber hose needs to adapt to harsh working conditions such as high pressure, high wear, corrosive media, and complex terrain, and its performance is directly related to the safety and efficiency of mining operations. This article will analyze the structural characteristics, core functions, and typical application scenarios.
1、 Structural characteristics of large-diameter rubber hose assembly for mining
1. Multi layer composite design ensures reliability
The mining rubber hose assembly usually adopts a three-layer composite structure of "inner rubber layer reinforcement layer outer rubber layer":
Inner rubber layer: High wear-resistant synthetic rubber (such as nitrile rubber NBR or polyurethane PU) is selected, with a thickness of 4-8mm. The surface is smooth to reduce fluid resistance and resist the erosion of solid particles (such as quartz sand and metal debris) in the slurry.
Enhancement layer: It is woven or wound from multiple layers of high-strength steel wire (tensile strength ≥ 2500 MPa), and the number of layers is adjusted according to the pressure level (for example, 6 layers of steel wire correspond to a working pressure of 35 MPa). Add aramid fiber layer in some special scenarios to enhance tear resistance.
Outer rubber layer: Made of weather resistant chloroprene rubber (CR) or chlorosulfonated polyethylene (CSM), with a thickness of 2-4mm, the surface is pressed with anti slip patterns or coated with polyurethane wear-resistant tape to resist rock friction and UV aging.
2. Customized connectors enhance connection security
According to DIN/ISO standards, the rubber hose is equipped with forged alloy steel flanges or quick couplings at both ends:
Flange joint: made of AISI 4140 alloy steel, surface galvanized or sprayed with epoxy resin, corrosion-resistant; The interface is sealed with an O-ring and crimped by a hydraulic press to ensure no leakage after 50000 pulse cycles.
Quick connector: suitable for frequent disassembly and assembly scenarios (such as mobile mineral processing equipment), with built-in self-locking buckle, capable of withstanding dynamic pressure of 30 MPa.
2、 Core functions and performance advantages
1. High pressure medium transportation
Mining rubber hoses have a wide working pressure range (10~60 MPa) and can transport various media such as water, mud, slag, acidic solutions, etc. For example, in underground drainage systems, DN300 (12 inch) rubber hoses can have a flow rate of up to 2000 m ³/h, meeting the needs of high flow drainage.
2. Wear resistance and impact resistance
In response to the wear of hard particles (Mohs hardness ≥ 7) in the slurry, silicon carbide (SiC) filler is added to the inner wall of the hose to increase wear resistance by 50%; The reinforcement layer adopts staggered winding technology to disperse impact energy and avoid local damage.
3. Corrosion resistant and explosion-proof design
Chemical protection: When transporting acidic mineral water (pH 2-5), the inner rubber layer is made of hydrogenated nitrile rubber (HNBR), which has three times higher acid and alkali resistance than ordinary NBR.
Anti static and flame retardant: The rubber hose is embedded with a copper wire conductive layer (resistance ≤ 1 Ω/m) to dissipate static electricity; Aluminum hydroxide flame retardant is added to the outer adhesive layer, with an oxygen index of ≥ 28%, which meets the MT/T 98-2012 mining safety standard.
4. Flexible adaptation to complex working conditions
The minimum bending radius of the rubber hose can reach three times the diameter of the pipe (such as a DN200 rubber hose with a bending radius of 600mm), suitable for narrow underground spaces; The working temperature range is -40 ℃~+120 ℃, suitable for high-altitude mining areas or high-temperature steam environments.
3、 Application Fields and Scenario Cases
1. Supporting drilling equipment
In the open-pit rock drill, DN150~DN250 rubber hoses are used to transport high-pressure water or foam, assist the bit cooling and rock cuttings discharge. For example, a copper mine used 52 MPa rubber hoses, which increased drilling efficiency by 20% and had a service life of 18 months.
2. Long distance transportation of slurry
At the beneficiation plant, DN500 large-diameter rubber hoses connect the flotation machine to the concentration tank, conveying high concentration slurry containing 60% solid particles. A certain iron mine in Australia uses double-layer steel wire wrapped rubber hoses, which have a 40% longer wear life than ordinary rubber hoses.
3. Hydraulic transmission of mining machinery
The hydraulic system of large excavators and loaders is equipped with DN32~DN80 rubber hoses, which transport fire-resistant hydraulic oil (HFD-R). The pulse pressure resistance performance has passed ISO 6803 certification, ensuring that the equipment can operate continuously for 2000 hours without any faults.