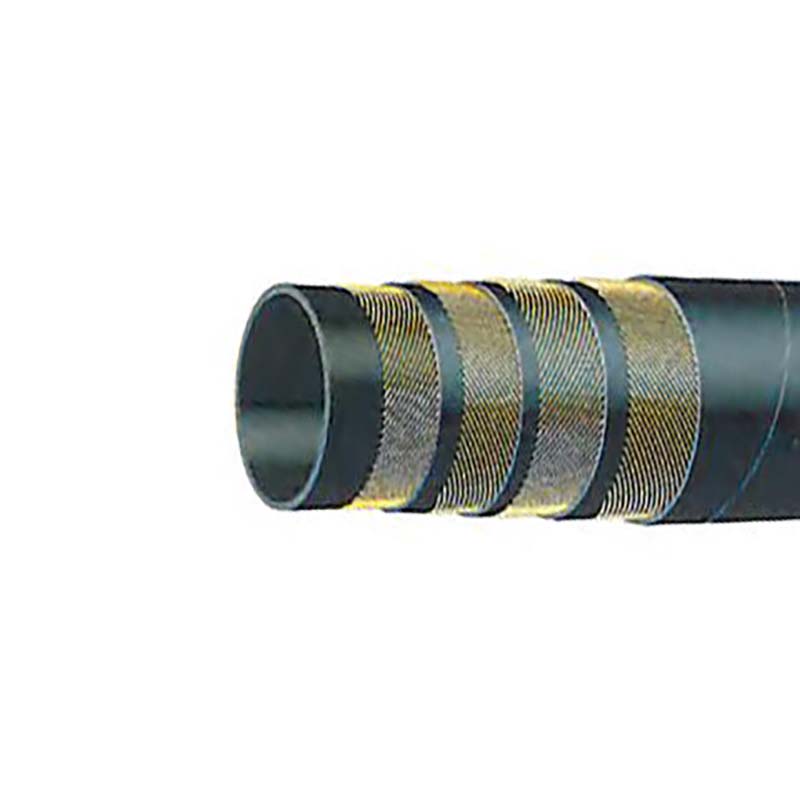
Guidelines for selecting rubber hoses for construction machinery
1、 Common materials for high-pressure rubber pipes
Internal adhesive layer material
Nitrile rubber (NBR): excellent oil resistance, suitable for hydraulic oil and mineral oil scenarios.
Chloroprene rubber (CR): resistant to ozone and aging, suitable for outdoor or high-temperature environments.
Ethylene propylene diene monomer (EPDM): water-resistant, steam resistant, used for hot and cold water or weak acid media.
Enhancement layer material
Polyester fiber thread: lightweight, high tensile strength, suitable for medium and low pressure scenarios.
Wire weaving/winding: ultra-high pressure resistance (above 40MPa), strong pulse resistance, used in construction machinery and hydraulic systems.
Outer adhesive layer material
Chloroprene rubber (CR): wear-resistant, UV resistant, and extends service life.
Chlorosulfonated polyethylene (CSM): resistant to chemical corrosion and suitable for industrial corrosive environments.
Natural rubber (NR): high elasticity, used in scenarios that require frequent bending.
2、 Key performance indicators of high-pressure rubber hose
Voltage resistance
Working pressure: 20-100MPa (steel wire reinforced type), blasting pressure is 3-4 times the working pressure.
Pulse performance: Through millions of pulse tests (ISO 6803 standard), ensure reliability under dynamic conditions.
Temperature adaptability
Temperature resistance range:- From 40 ℃ to+120 ℃ (EPDM material can reach+150 ℃), it is not easy to soften at high temperatures and remains flexible at low temperatures.
Dielectric resistance
Oil/acid/alkali resistance: NBR is oil resistant, EPDM is acid/alkali resistant, and the material should be selected according to the conveying medium.
Anti swelling property: The volume expansion rate of the hose after contact with the medium is ≤ 5% (ASTM D471 standard).
Mechanical performance
Flexibility: Small bending radius (such as 1:5 pipe diameter), suitable for complex pipeline layouts.
Wear resistance: The outer rubber hardness is ≥ 70 Shore A, reducing the risk of external wear.
Durability
Anti aging: through ozone aging and thermal oxygen aging tests (GB/T 3512 standard), the service life can reach 5-10 years.
3、 Matching scenarios of materials and performance
Construction machinery (such as excavators): steel wire winding+CR outer rubber, resistant to high pressure, impact, and external wear.
Chemical equipment: EPDM inner rubber+CSM outer rubber, resistant to corrosive media and chemical erosion.
Mining hydraulic system: NBR inner rubber+steel wire reinforcement, resistant to oil and high-pressure pulses.
4、 Selection and maintenance suggestions
Selection principle: Match materials comprehensively based on pressure level, medium type, and environmental temperature.
Usage taboos: Avoid overpressure, excessive bending, or contact with incompatible chemicals (such as NBR, which is not resistant to strong acids).
Maintenance focus: Regularly check for cracks in the outer rubber layer and leaks in the joints, and replace aging rubber hoses in a timely manner.