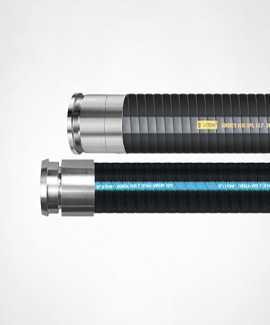
Flange connection vs. quick connector: 8-inch rubber hose
8-inch rubber hose (nominal inner diameter 200mm) is a commonly used fluid transportation pipeline in the industrial field. Its design parameters, material characteristics, and application scenarios are all focused on high flow rate, high pressure, corrosion resistance, and other requirements. The following is a systematic analysis from four dimensions: specification parameters, material types, application scenarios, and selection suggestions:
1、 Specification parameters
Nominal inner diameter: The 8-inch rubber hose corresponds to a metric size of DN200 (200mm), which complies with the pipeline size specifications of the International Organization for Standardization (ISO).
Wall thickness range: Depending on the working pressure and medium characteristics, the wall thickness is usually between 8mm and 25mm. For example, the wall thickness of high-pressure oil transportation hoses can reach over 20mm, while the wall thickness of low-pressure drainage hoses may be 8-12mm.
Work pressure level:
Low pressure type (≤ 1.6MPa): suitable for agricultural irrigation, urban drainage and other scenarios, mainly made of natural rubber.
Medium pressure type (1.6-10MPa): used for sand discharge in mines and industrial wastewater treatment, often using a fabric reinforcement structure.
High pressure type (≥ 10MPa): For high-pressure environments such as oil drilling and hydraulic systems, multiple layers of steel wire weaving or winding reinforcement layers are required.
Length customization: The standard length is usually 10m or 20m, but it can be customized according to engineering requirements (such as 50m continuous roll pipe).
2、 Material type and characteristics
Natural rubber (NR)
Advantages: Excellent elasticity, strong wear resistance, suitable for transporting non corrosive media such as mud and mineral sand.
Limitations: Poor oil resistance, prone to swelling when exposed to oil for a long time.
Nitrile rubber (NBR)
Advantages: Outstanding oil resistance, suitable for media such as fuel and hydraulic oil, with a temperature range of -30 ℃ to+120 ℃.
Application: Hydraulic systems for construction machinery, oil field water injection pipelines.
Chloroprene rubber (CR)
Advantages: Excellent weather resistance and flame retardancy, suitable for outdoor environments or fire protection systems.
Limitations: Poor cold resistance and easy hardening at low temperatures.
Fluororubber (FKM)
Advantages: High temperature resistance (up to 250 ℃), strong acid and alkali resistance, suitable for corrosive media in chemical industry.
Cost: The price is 3-5 times that of ordinary rubber and is only used for special working conditions.
Enhancement layer material
Steel wire weaving/winding: improves pressure resistance, such as 6-layer steel wire winding rubber hose with a pressure resistance of over 40MPa.
Fiber weaving: reduces weight and is suitable for light load and low voltage scenarios.
3、 Application scenarios
Mining and Engineering
Sand flushing hose: used for sand flushing in tailings ponds and dredging in rivers, it needs to be wear-resistant and impact resistant, with a wall thickness usually ≥ 15mm.
Spraying rubber hose: For tunnel support concrete transportation, it is required that the inner wall be smooth and resistant to high-pressure pulses.
Petroleum and Chemical Industry
Oil delivery hose: For crude oil transportation in refineries, it needs to be resistant to high temperatures (above 150 ℃) and aromatic hydrocarbon corrosion.
Acid alkali rubber hose: used for transporting hydrochloric acid and sulfuric acid in chemical plants, lined with fluororubber or polytetrafluoroethylene.
Agriculture and Water Conservancy
Irrigation hose: a drip irrigation system for farmland, which needs to be lightweight and resistant to aging, often made of PVC/rubber composite material.
Drainage hose: Urban flood prevention and rescue require rapid deployment and resistance to negative pressure (such as -0.09MPa).
Naval Architecture and Marine Engineering
Cabin bottom drainage hose: resistant to seawater corrosion and UV radiation, requiring certification from the International Maritime Organization (IMO).
Oil tanker loading and unloading hose: It must meet the API 17K standard, withstand pressure of 25MPa or above, and burst pressure ≥ 4 times the working pressure.
4、 Selection suggestions
Clarify the characteristics of the medium
Fluorine rubber or PTFE lined rubber hoses are preferred for corrosive media such as acid and alkali.
High temperature media (such as steam) should use silicone rubber or ethylene propylene diene monomer (EPDM).
Determine work pressure
The hydraulic system needs to select the hose pressure resistance level based on 1.5 times the maximum pressure of the system.
Dynamic working conditions (such as pulse pressure) require consideration of fatigue life, and it is recommended to choose a steel wire winding reinforcement structure.
Environmental adaptability
Outdoor use requires evaluation of the aging effects of ultraviolet and ozone on rubber, and it is recommended to add carbon black anti-aging agents.
Cold resistant rubber (such as chloroprene rubber SBR) should be selected for low temperature environments (below -40 ℃).
Connection method matching
Flange connection: Suitable for high-pressure large-diameter rubber hoses and must comply with the GB/T 9119 standard.
Quick connector: Easy to disassemble frequently, choose a model that matches the inner diameter of the hose (such as DN200 hose with 200mm diameter connector).