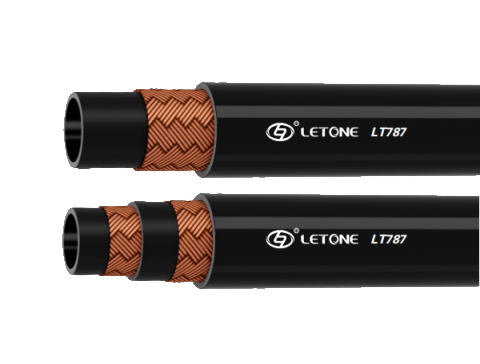
5 core performance requirements for marine air rubber hoses
Marine air rubber hoses are key components in ship air delivery systems, and their design must meet strict requirements such as pressure resistance, weather resistance, and corrosion resistance. The following provides a detailed analysis from five dimensions: structural composition, performance parameters, application scenarios, selection criteria, and maintenance management:
1、 Structural composition and material properties
Multi layer composite structure
Inner rubber layer: Made of oil resistant and ozone resistant synthetic rubber (such as NBR or SBR) to ensure long-term contact with compressed air without swelling or aging.
Enhancement layer: High strength synthetic fiber weaving or steel wire winding layer, providing anti explosion support, and some models are equipped with conductive wires to eliminate static electricity risks.
Outer rubber layer: black/yellow/blue weather resistant rubber, with wear resistance, UV resistance, and flame retardant properties. Some products have passed IMO fire certification.
Sealing and Connection Design
The end of the pipe is connected with threaded joints or flanges, which are compatible with the standards of ship pipeline systems.
Install metal sheaths at critical locations to prevent mechanical damage from causing air leakage.
2、 Core performance parameters
Pressure and explosion safety
Working pressure range: 0.8~1.6MPa (some high-pressure models can reach 2.5MPa).
The blasting pressure is more than 4 times the working pressure to ensure safety under extreme working conditions.
Temperature tolerance
Conventional model: -30 ℃ to+80 ℃; The special cold resistant type can be as low as -50 ℃ and is suitable for polar navigation ships.
Bending and fatigue life
The minimum bending radius is ≤ 5 times the outer diameter to reduce installation space occupation.
Simulate the reliability of ship vibration environment through dynamic fatigue testing (such as 100000 cycles of pulse pressure).
3、 Typical application scenarios
Main and auxiliary system
Connect the air compressor to the air storage tank, and deliver compressed air to the starting device, pneumatic valves, and other equipment.
Cabin ventilation and sealing
Used for connecting ventilation ducts or as a key component of cabin pressure balancing systems to prevent seawater backflow.
Adaptation to special working conditions
Inert gas transportation (such as nitrogen) requires the rubber layer inside the hose to have low permeability.
Chemical resistant models (such as those with EPDM rubber layers) are suitable for auxiliary systems in chemical tankers.
4、 Key elements of selection
Media compatibility
Choose the inner rubber material based on the type of gas being transported: NBR can be selected for compressed air, and FKM should be used for oil mist environments.
Pressure and flow matching
Calculate the required flow rate of the system (Q=v × A, where v is the flow velocity and A is the cross-sectional area of the pipe), and select a suitable inner diameter (such as DN25~DN100).
The high-voltage system needs to be equipped with a steel wire winding reinforcement layer, while the low-voltage system can use a fiber weaving layer to reduce costs.
Environmental adaptability
The exposed area of the deck needs to use a UV resistant outer layer, and the high-temperature area inside the engine room needs to enhance its heat resistance.
Explosion proof areas (such as near oil tanks) must use models with conductive wires and a resistance of ≤ 10 ⁶ Ω/m.
5、 Maintain management standards
regular inspection
Monthly inspection of appearance: for cracks, bulges, or peeling of the outer adhesive layer.
Conduct stress testing every six months: hold the pressure at 1.5 times the working pressure for 5 minutes, and observe the changes in the pressure gauge reading.
Replace standard
Replace immediately if the following situations occur:
The reinforcement layer is exposed or the steel wire is broken.
The minimum burst pressure is below 80% of the standard value.
The service life exceeds the manufacturer's recommended lifespan (usually 5-8 years).
Storage requirements
Avoid light and dry environment, with temperature controlled between 0~35 ℃.
When storing coils, the diameter should be ≥ 20 times the outer diameter to avoid deformation caused by long-term compression.