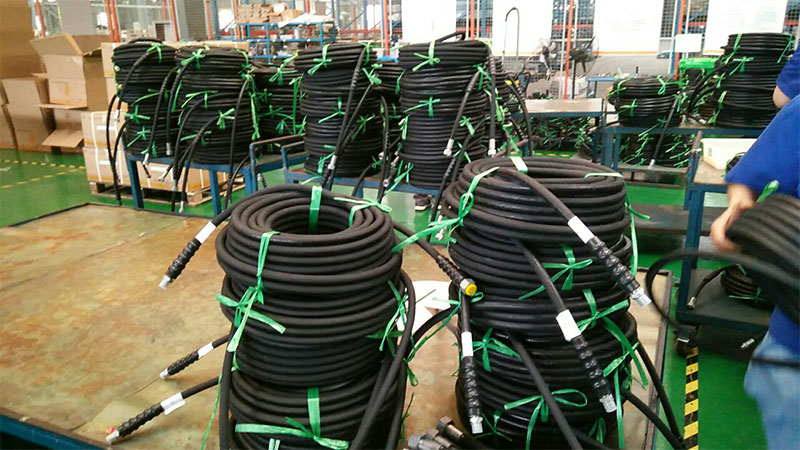
Double layer steel wire wear-resistant rubber hose
The core of a flange high-pressure hose lies in the integration of the flange joint and the hose body, which requires a balance between pressure bearing capacity, corrosion resistance, and dynamic fatigue life:
Flange joint design:
Material selection: forged steel (ASTM A105), stainless steel (316L) or alloy steel (Inconel 625), surface galvanized or sprayed with epoxy resin, salt spray corrosion resistance grade ≥ C5-M (ISO 12944).
Sealing form: Flat flange (FF) with rubber gasket (NBR/FKM), concave convex flange (RF) with metal wrapped gasket, ensuring a leakage rate of<1 × 10 ⁻⁶ Pa · m ³/s at 30MPa (ASME B16.5 standard).
Bolt pre tightening force: calculated according to ASME PCC-1, controlled by torque+angle method to avoid flange deformation caused by overload.
Hose body structure:
Inner rubber layer: Nitrile rubber (NBR) or Fluorine rubber (FKM), with a thickness of 3-6mm, resistant to oil and acid alkali (pH 2-12), suitable for temperatures ranging from -30 ℃ to 120 ℃.
Enhancement layer: 4-6 layer high carbon steel wire (diameter 0.25~0.4mm) is interlaced at 54 °~56 °, with a tensile strength of ≥ 2500N/mm ² and a burst pressure of ≥ 4 times the working pressure.
Outer rubber layer: chloroprene rubber (CR) or polyurethane (PU), UV resistant and wear-resistant, with a surface added with a conductive layer (resistance ≤ 1 × 10 ⁶ Ω), in compliance with ATEX explosion-proof requirements.
Key process control:
Compression molding: Using a CNC hydraulic press, the compression accuracy is ± 0.02mm, ensuring that the tensile strength between the flange and the hose is ≥ 80% of the hose body.
Sulfurization process: segmented temperature controlled vulcanization (150 ℃~170 ℃), eliminating internal stress and improving interlayer adhesion strength (≥ 8kN/m).
2、 Performance Verification Standards: High Voltage, Pulse, and Extreme Environment Testing
Flange high-pressure hoses must undergo rigorous laboratory testing and industry certification to ensure their reliability under complex working conditions
Static pressure test:
Explosion pressure test (ISO 1402): Hold at 1.5 times the working pressure for 5 minutes without leakage or structural deformation; Gradually increase the pressure to 4 times the pressure until failure occurs, and record the critical value.
Axial tensile test (EN 14412): Apply a tensile force of ≥ 15 times the nominal inner diameter of the hose, with a displacement of ≤ 5% and no separation between the flange and the hose.
Dynamic performance verification:
Pulse fatigue test (ISO 6803): Cycle 100000 times (frequency 1Hz) under pressure of 0-40MPa, with flow fluctuation of ≤± 3%, and no permanent damage to the flange sealing surface.
Bending fatigue test: The hose was dynamically swung with a bending radius of 6 times the diameter of the pipe (± 45 °, frequency 0.5Hz), and after 50000 cycles, there were no broken wires in the reinforcement layer and no loose joints.
Environmental adaptability assessment:
High and low temperature alternating test (IEC 60068-2-14): -40 ℃ (2h) ↔ After 20 cycles at 120 ℃ (2h), there were no cracks in the adhesive layer, and the sealing performance remained at the original design value.
Chemical resistance test (ASTM D471): Soak in 10% H ₂ SO ₄, diesel, and hydraulic oil (HM-46) for 168 hours, with a volume change rate of ≤± 10% and a hardness change of ≤± 15 Shore A.
Industry certification: Passed API 16C (drilling equipment), EN 1762 (flammable fluids), DNV-GL (ships) certification, adapted to compliance requirements in different fields.
3、 Industrial scenario selection practice: adaptation to working conditions and risk avoidance
The selection of flange high-pressure hoses should be based on the characteristics of the medium, pressure rating, and installation environment to avoid failure caused by overload or corrosion
High pressure mud transportation for oil drilling:
Characteristics of working conditions: high sand content (≤ 15%), frequent pressure fluctuations (20-35MPa), and H ₂ S corrosion risk.
Selection plan: Inner layer FKM+316L steel wire reinforcement, flange with Inconel 625 wrapped gasket, certified by API 16C, it is recommended to test the flange bolt pre tightening force every 500 hours.
Acid alkali medium transmission in the chemical industry:
Working condition characteristics: strong corrosion (pH 1-14), large temperature gradient (-20 ℃~80 ℃).
Selection plan: Inner PTFE lining+EPDM outer adhesive layer, flange made of 316L material+graphite gasket, with a 20% margin reserved for working pressure to avoid sealing failure caused by acid crystallization.