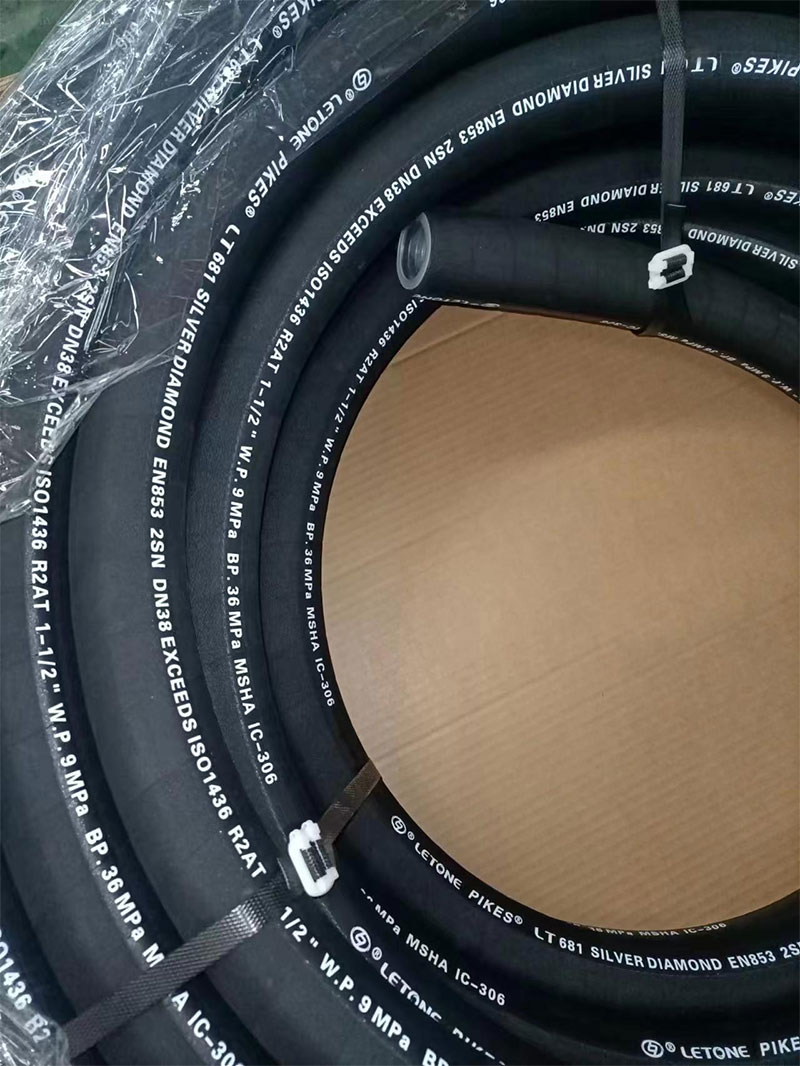
Analysis of High Pressure Sandblasting Rubber Hose Materials
The double-layer steel wire wear-resistant rubber hose is a key transmission component in high-pressure, high wear industrial scenarios such as mining transportation, oil drilling, and concrete spraying. Its unique reinforcement layer structure endows it with excellent compressive, impact, and fatigue resistance properties. This article conducts professional analysis from three aspects: material and structural design, core performance testing, typical applications, and selection guidelines, providing technical references for engineering applications.
1、 Material and structural design: Double layered steel wire weaving reinforcement achieves a balance between strength and flexibility
The double-layer steel wire wear-resistant rubber hose adopts a multi-layer composite structure design, which takes into account the requirements of wear resistance, high pressure resistance, and torsion resistance:
Internal adhesive layer:
Material selection: Made of ultra wear-resistant synthetic rubber (such as SBR, NBR) or polyurethane (PU), with a thickness of 4-8mm and a Shore hardness of 70-90A, ensuring high wear resistance and tear resistance.
Functional characteristics: Smooth surface to reduce abrasive adhesion, resistant to medium erosion (such as acid, alkali, oil), suitable for conveying fluids containing solid particles such as mortar and mineral powder.
Enhancement layer:
Double layer steel wire weaving: The inner layer of steel wire is tightly woven at an angle of 54 °~56 °, and the outer layer is woven at a reverse angle, forming a mesh like compressive structure with a tensile strength of ≥ 60MPa and a burst pressure of up to 4 times the working pressure.
Process requirements: Steel wire diameter of 0.3~0.5mm (such as 304 stainless steel or copper plated steel wire), weaving density ≥ 95%, ensuring uniform force and resistance to pulse pressure impact.
Outer adhesive layer:
Weather resistant design: Made of chloroprene rubber (CR) or EPDM, with a thickness of 2-4mm, resistant to UV and ozone aging, suitable for outdoor or underground environments ranging from -40 ℃ to 120 ℃.
Key design parameters:
Bending radius: ≥ 6 times the diameter of the pipe (e.g. DN50 rubber hose requires ≥ 300mm), to prevent deformation of the steel wire layer caused by bending;
Joint process: Adopting triple compression sealing (compliant with SAE 100R2AT standard) to avoid detachment or leakage under high pressure.
2、 Core performance testing: reliability verification in harsh environments
The double-layer steel wire wear-resistant rubber hose needs to pass multiple international standard tests to ensure its stability under extreme working conditions:
Voltage and impact resistance performance:
Burst pressure test (ISO 1402): No rupture for 3 minutes at 4 times the rated pressure (e.g. 30MPa);
Pulse fatigue test (ISO 6803): cycled 200000 times with pressure fluctuations ranging from 0 to 30 MPa, without leakage or structural damage.
Wear resistance verification:
Abrasive erosion test (ASTM D5964): After 100 hours of erosion with a slurry containing 30% quartz sand (particle size 0.5-1mm) (flow rate 3m/s), the inner layer wear is ≤ 0.08g/cm ³;
Bending wear test: The rubber hose simulates dynamic wear in a bent state, with no cracks or peeling on the inner surface.
Environmental adaptability:
Temperature resistance: No brittle fracture when bent at -40 ℃, and the hardness change of the outer adhesive layer at 120 ℃ is ≤ 15 Shore A;
Corrosion resistance: Soak in a 5% sulfuric acid solution for 48 hours, with a volume expansion rate of ≤ 5%;
Oil resistance (ASTM D471): After soaking in diesel for 72 hours, the tensile strength retention rate of the outer coating layer is ≥ 80%.
Industry certification: Through MSHA (Mine Safety Certification) and API 16C (Petroleum Drilling Standard) certification, ensure safety compliance in the mining and energy fields.
3、 Typical Applications and Selection Guidelines
Double layer steel wire wear-resistant rubber hoses are widely used in industrial scenarios with high wear and high pressure. The selection should be based on specific working conditions:
Mining slurry transportation:
Characteristics of working conditions: high abrasive concentration (including iron ore and tailings), large pressure fluctuations (15-25MPa);
Selection suggestion: The inner layer is reinforced with polyurethane and steel wire, with a rated pressure of ≥ 25MPa and a length of ≤ 50m to reduce pressure loss.
High pressure water injection for oil drilling:
Working condition characteristics: sand containing drilling fluid flushing, high temperature underground (≤ 100 ℃);
Selection suggestion: Choose NBR inner layer+316 stainless steel wire, resistant to hydrogen sulfide corrosion, certified by API 16C.
Concrete wet spraying support:
Working condition characteristics: aggregate particle size ≤ 15mm, frequent pulse pressure (10-20MPa);
Selection suggestion: Inner layer thickness ≥ 6mm, bending radius ≥ 8 times the pipe diameter, matched with rotary joints to reduce torsional stress.
Selection principle:
Pressure matching: working pressure ≤ 70% of the rated pressure of the hose;
Media compatibility: EPDM outer layer is preferred for acidic media, and NBR inner layer is preferred for oily media;
Length optimization: For every 10m increase in length, the pressure loss increases by 0.1~0.3MPa, which needs to be adjusted according to the pumping power.