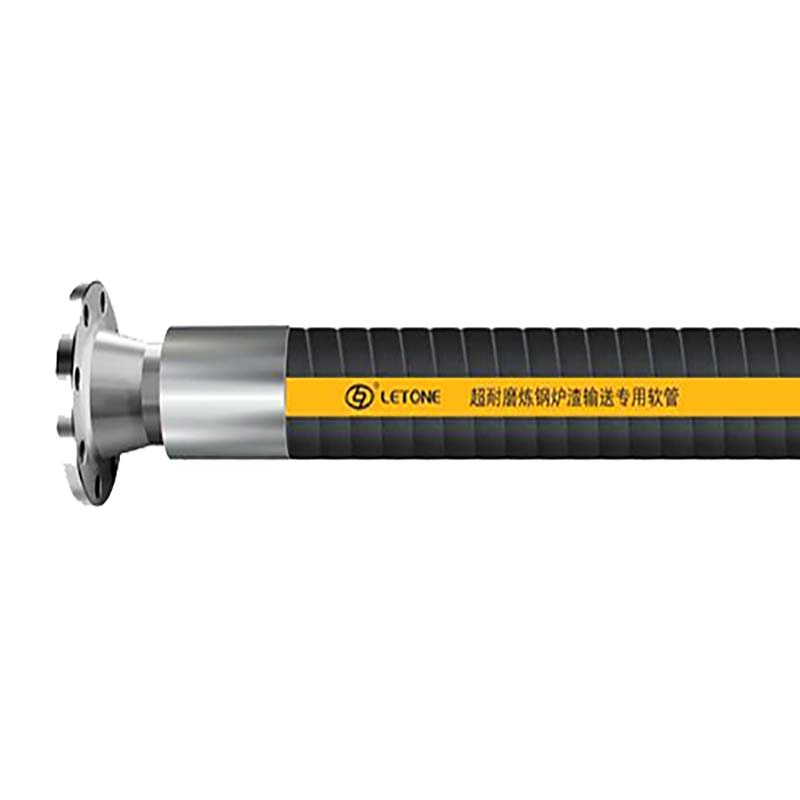
Design of Structural Materials for High Pressure Sandblasting Rubber Hose
High pressure sandblasting hose is a core equipment component in the field of industrial surface treatment (such as rust removal, cleaning, coating pretreatment), and its performance directly determines the efficiency, safety, and equipment life of sandblasting operations. This article analyzes from three aspects: material and structural design, performance requirements and testing standards, typical application scenarios and selection suggestions, providing professional references for engineering and technical personnel.
1、 Material and structural design: multi-layer composite reinforcement to ensure stability in high-pressure environments
The high-pressure sandblasting hose needs to operate stably for a long time under extreme working conditions (pressure 20-50MPa, abrasive impact, high/low temperature), and its internal structure adopts a multi-layer composite design:
Inner rubber layer: Usually made of ultra wear-resistant polyurethane (PU) or nitrile rubber (NBR), with a thickness of 3-6mm, it needs to have the following characteristics:
High wear resistance: resistant to continuous impact from abrasives such as quartz sand and steel balls;
Chemical corrosion resistance: resistant to oil stains and weak acidic and alkaline media erosion;
Low surface adhesion: reduces abrasive residue and lowers the risk of clogging.
Reinforcement layer: High strength synthetic fibers (such as aramid, polyester) or steel wire woven layers are used, and the number of layers is adjusted according to the pressure level (such as 4-6 layers for 30MPa), ensuring a tensile strength of ≥ 50MPa and a burst pressure of ≥ 3 times the working pressure.
Outer rubber layer: Made of weather resistant chloroprene rubber (CR) or EPDM rubber, with a thickness of 2-4mm, it needs to be resistant to ultraviolet radiation, ozone aging, tear and puncture, and suitable for harsh outdoor environments.
Design key point: The bending radius of the hose should be ≥ 8 times the diameter of the pipe to avoid inner layer wear caused by bending; The joint adopts double-layer crimping technology (such as SAE 100R series standard) to prevent detachment under high pressure.
2、 Performance requirements and testing standards: Reliability verification under harsh operating conditions
The performance of high-pressure sandblasting hose needs to be verified by international standards to ensure its compliance with industrial safety regulations:
Voltage resistance performance:
Explosion pressure test (ISO 1402): The rubber hose must withstand an instantaneous pressure of more than 3 times the rated pressure (e.g. a 30MPa rubber hose must pass a 90MPa test);
Pulse fatigue test (ISO 6803): No leakage after 100000 cycles under pressure fluctuations (0-30 MPa).
Wear resistance:
Wear test (ASTM D5964): Impact the inner wall with quartz sand (particle size 0.5-1mm), and the wear should be ≤ 0.1g/cm ³ (tested for 100 hours).
Environmental adaptability:
Temperature resistance range: Rubber hose hardness change ≤ 10 Shore A at -40 ℃~120 ℃;
Oil resistance (ASTM D471): Soak in diesel for 72 hours, with a volume expansion rate of ≤ 10%.
Industry certification: High quality rubber hoses must pass MSHA (Mine Safety Certification) or DNV (Ship Industry Certification) to ensure compliance in high-risk scenarios such as mines and ships.
3、 Typical application scenarios and selection suggestions
High pressure sandblasting hoses are widely used in industrial fields that require efficient surface treatment, and different scenarios require targeted selection:
Shipbuilding and Maintenance:
Requirement: Rust removal of ship hull steel plates (Sa2.5 cleanliness level), coating pretreatment;
Selection: Choose a steel wire reinforced rubber hose (such as 30MPa pressure rating) with a length of 15-30m, paired with a rotary joint to adapt to narrow cabin operations.
Automotive Manufacturing and Aerospace:
Requirement: Sandblasting strengthening of aluminum alloy parts and composite material surfaces;
Selection: The inner layer is made of polyurethane material (with better wear resistance than rubber), and the outer layer is covered with an anti-static layer to avoid the risk of sparks.
Petrochemical pipeline maintenance:
Requirement: Cleaning the inner wall of the pipeline (removing coking and rust);
Selection: NBR inner rubber hose with oil and acid alkali resistance, equipped with quick couplings (such as Camlock) to improve pipe replacement efficiency.
Selection principle:
Pressure matching: The rated pressure of the sandblasting machine is ≤ 80% of the working pressure of the hose;
Length optimization: For every 1m increase in length, the pressure loss is about 0.02MPa, which needs to be adjusted according to the equipment power;
Compatibility of connectors: Prioritize the use of universal standards (such as ISO 7241-A type) to reduce maintenance costs.